RWTH Aachen, IME Process Metallurgy ans Metal Recycling Institute
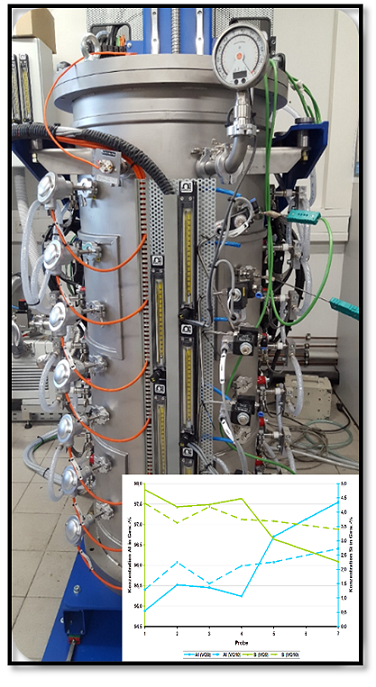

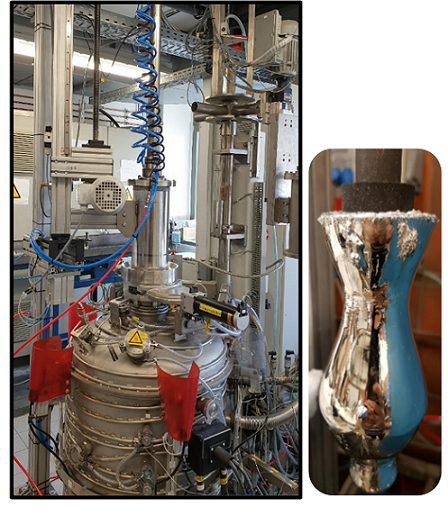
The IME is one of Europe's leading development centers for environmentally friendly processes in metal recycling. Between 1996 and 2003, it coordinated work on metal recovery and further processing as a founding member of SFB 525 "Resource-oriented overall consideration of material flows of metallic raw materials". Since 2000, twelve large-scale European and nationally funded research projects have been carried out in the field of "production-integrated environmental protection". With 1,000 m² of experimental space, process chains can be realized up to demonstration scale. Core competencies are the development of sustainable environmentally friendly and cost-efficient processes for the production, cleaning and recycling of metallic materials. The research priorities of the IME are inevitably subject to the constantly changing needs and priorities of political requirements as well as those of the associated industrial companies. Almost the entire range of metals is covered, with current emphasis on Ti, Si, Ge, Sb, Al, Mg, Cu as well as the rare earths. In addition, the IME has been involved for years in research and teaching on the subject of "Removal of metallic impurities from melts", in particular in order to achieve extremely high degrees of purity. Currently, the IME's "Pure Metals Group" is working on the high-purity refining of aluminum, magnesium, antimony as well as germanium and tellurium. In this context, the IME has been fundamentally researching three methods for the production of high-purity metals. A static crystallization furnace, which is divided into seven resistance zones that can be individually controlled by a programmable controller and brought to the desired temperature. This allows a predetermined cooling profile to be run automatically, with cooling occurring only by regulating the power introduced and no additional external cooling is used. The impurities with a partition coefficient smaller than one are to remain in the residual melt, while those with a partition coefficient larger than one are enriched at the bottom of the crucible, leaving a refined block of the target metal after later removal of the bottom and top cover (see Fig. 1).
A horizontal zone melting system (Fig. 2), controlled by means of an inductive power of max. 45 kW, allows a feed rate of max. 1.99 mm/min and has so far been successfully used to purify aluminum from 3N to 4N. Here, the complexity of controlling the degree of purity due to the length of the melting zone and the high time requirement of the process led to the idea of exploring the "cooling finger" methodology. The "Pure Metals" working group at IME is therefore also working on the subject of metal refining using cooling fingers (see Fig. 3). The precise control of the temperature gradient, itself influenced by, among other things, the rotation of the finger as well as the cooling gas flow, is the most important challenge in the development of this methodology, because these parameters have a direct effect on both the shape of the crystallization and the growth rate of the crystallized material, and thus on the efficiency of impurity removal.