Fraunhofer Institute for Manufacturing Technologies and Advanced Materials IFAM, Branch Lab Dresden
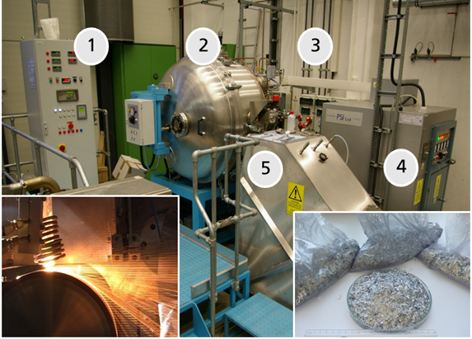
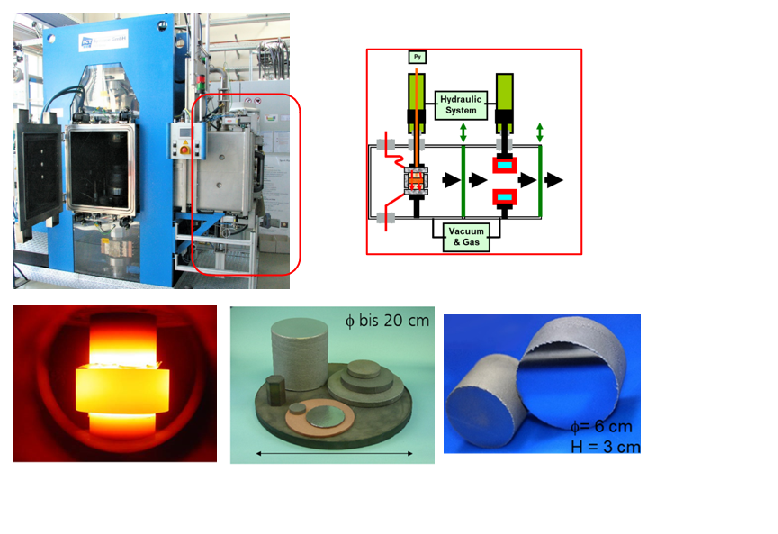
The Fraunhofer Institute for Manufacturing Technology and Applied Materials Research IFAM, Dresden branch, is the largest European research institution in the field of powder metallurgy with a staff of approx. 74. IFAM has been working for many years in the field of powder metallurgical production and shaping of thermoelectric (TE) (silicides, skutterudites, clathrates, Bi2Te3) and magnetocaloric materials (MK) (La(Fe,Si)13). In addition to thermoelectrically active high-temperature materials based on Mg2Si and Mn11Si19, the focus is also on room-temperature materials based on Bi2Te3. The technological focus of the current work is on questions concerning the upscaling of processes and the production and manufacturing of advanced TE and MK materials and their recycling. IFAM has an extensive infrastructure covering the entire value chain, from the production of master alloys to the manufacture of sintered semi-finished products on a production-relevant scale. The necessary infrastructure can also be used for recycling the materials:
- Melt spinning with melting capacity up to 1 liter per batch for the production of fine-grained, nanocrystalline or amorphous feedstocks as ribbons or flakes e.g. from Bi2Te3 (Fig. 1).
- High energy mills (up to kg-batch) for the conversion of the starting materials into sinterable powders
- Spark Plasma Sintering (SPS) for the production of sintered semi-finished products with diameters up to 20 cm and heights of several centimeters (Fig. 2)
- Furnace systems for heat treatment, usable space up to approx. 35 liters and temperature up to max. 2200 °C under e.g. air, Ar, H2, vacuum
In addition to the technological infrastructure, IFAM has comprehensive analytical equipment for materials research in the manufacturing, production or recycling process, including metallography, XRD and chemical and thermal analysis.
IFAM is involved in various public projects dealing with TE materials (Magman (BMBF), TekoCar (BMBF), NEAT(EU), WiSE (BMBF), Heat4Efficiency (BMWi), Nanostructuring of clathtrates-I and -II (DFG SPP1386), Dimensionality, nanostructure of Bi2Te3-I and -II (DFG SPP 1386)) or MK (DRREAM (EU), MagCon (FhG-Intern)). In these projects a large experience on the chemical behavior of these compounds has been gained and the results have been published in professional journals or presented in international meetings. In the field of R&D activities on rare earth recycling, IFAM has patented a method for the recovery of Nd or Nd2O3 from starting mixtures or scrap containing Nd-Fe-B (PCT/EP2013/067264).